Areas to focus on when improving the efficiency of pork production.
Pig Rearing, Fattening and Breeding
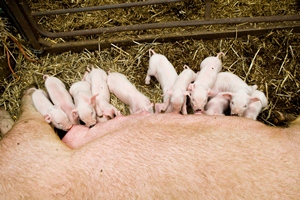
Production of pork produces approximately half the GHGs per kilo of meat compared to beef or lamb since pigs are monogastric and produce only a fraction of the methane of ruminants. However the majority of UK beef and lamb are fed from land that is not suitable for any other agricultural cropping and which is sequestering carbon, while extensive and especially intensive pork production utilises arable crops to produce food with far less efficiency than the direct consumption of those crops. Traditionally pig production was an efficient means of converting inedible waste food and bi-products into food, with current legislation on swill feed meaning that this is not at present possible.
GHG emissions from pig rearing systems are primarily nitrous oxide (N2O) which in most studies accounts for about half of all GHG emissions with the remainder being equal between methane (CH4) and carbon dioxide (CO2).
Emissions from pig production occur from two main sources, the underlying enteric emissions produced when food is broken down during the rearing process (11% GHG contribution) and during manure management. For pig production 20% of the total GHG contribution is from nitrous oxide and a further 69% from methane released from manure.
Feeding
Approximately 50 – 70 % of all GHG emissions are from the growing (and to a lesser extent any processing and transporting) of feedstuffs, this is partly from the production and application of nitrogen fertilisers and partly from the soil processes and GHG emissions inherent in most crop husbandry systems. If the ration contains soya grown overseas is can have much higher emissions associated with its production.
Ensuring optimum feed conversion efficiency is a key aim for all pig farmers along with achieving the optimum productivity from your production system. So attention to feed analysis and diet, minimizing waste and attention to factors that may reduce feed conversion efficiency are standard husbandry practices.
However as the majority (60–70 %) of emissions are from N2O, reducing the amount of crude protein (CP) in the ration formulation can also have a positive effect on reducing N2O emissions. In pig rearing approximately 25–40% of all the nitrogen (N) contained in feed rations is converted into proteins and used in animal growth, the other 60–75% is excreted. The higher the levels of N in the manure, the greater the potential there is for ammonia (NH3) emissions, which can be oxidised to N2O and therefore subsequent N2O emissions. A diet with lower levels of CP will potentially result in lower N2O emissions. There have been a number of studies that have shown that reducing the CP level of the diet by 3% – a 17% CP down to a diet with 14% CP – and supplementing with appropriate amino acids (to ensure sufficient levels of essential amino acids for achieving full growth potential), can result in a reduction of 30% less N excreted, by the animal and up to 40% reduction in N2O emissions from the manures as slurry or solids.
Manures
There are a variety of strategies that can be employed to reduce the amount of N2O and CH4 emissions associated with manure storage and application. The proportion of GHG emissions from each stage will depend very much on the system adopted and the weather and so can be very different between farms and in each year.
Storage
Ensuring that there is adequate slurry storage and land for spreading on so that applications can be best matched to crop growth and nutrient requirements is fundamental.
During storage it is possible to reduce losses of CH4 and N2O through specific management of the slurry store and muck heaps, but the amounts of emissions that can be reduced are not clear. Bacterial activity is responsible for the production of CH4 and ammonia (NH3) – which is then available to be oxidised to N2O – and is dependent on a range of factors especially, pH, temperature and the degree of aeration of the store.
The composition of manure heaps, the moisture content and the amount of airflow over the storage will also affect rates of emissions. Covering the surface of a slurry store/muck heap with a plastic sheet has shown to reduce emissions (covering with chopped straw or woodchip doesn’t). Acidifying the slurry store reduces the bacterial activity and has been shown to significantly reduce NH3 and CH4 production. Cooler temperatures and regular turning of manure heaps also reduces emissions.
Muck spreading
Best practice during application is generally considered to be always cost effective as it makes maximum use of the nutrients in the manures with minimum GHG losses. Matching nutrients in the slurry to the crop requirements (only spreading slurry in the growing season), not spreading on water logged soils, using a trailing shoe to place the slurry next to the soil rather than spreading onto of land/grass will all significantly reduce N2O emissions.
Anaerobic digestion
Because pig slurry is higher in undigested feedstuff than cattle slurry, it is more suited to anaerobic digesters. Using the slurry in an AD plant gives a triple win as not only are GHG emissions from slurry storage cut to almost zero, the resulting digestate releases less N2O on application than slurry or FYM, however applied, and also the carbon in the slurry is used to produce methane which is then captured in the AD plant and used as a renewable source of energy.
Reducing CO2 emissions and energy savings
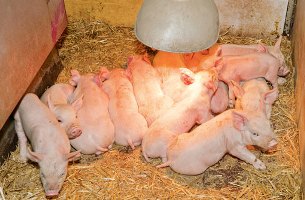
The more intensive the production system, the higher the direct energy requirements, the larger the % of GHG emissions as CO2 and the greater the potential to save money and GHG emissions from energy efficiency measures.
Heating and ventilation are responsible for most energy used in intensive systems. An energy audit will show how much energy is used, where, how your unit compares to similar farms, the areas where efficiencies can be put into place and likely costs and saving from such works. Good insulation, regular equipment maintenance, monitoring actual energy use against expected use and use of energy saving technologies such as heat exchange systems can all help with reducing energy usage and lowering GHG emissions. Whenever significant investment is being planned, looking at the smart ways to reduce GHG emissions, through the redesign of the system along with reducing energy consumption will be a valuable investment and should be a priority in any forward planning.